1. Context & Problem
- APC Holdings is the middle person between companies seeking machine component replacements and the factories producing them.
- Currently, all information is handled through physical papers, excel sheets, white boards, emails and phone calls.
- This process has often led to miscommunication, production delays and frustration across every level of the organization.
- Therefore, we were requested to create a custom ERP solution to track orders and manage tasks across the product’s lifecycle.
2. What We Did
- Interviewed stakeholders across multiple roles.
- Affinity analysis of interview data.
- Artifact collection.
- Mapped product lifecycle from order creation to shipping.
- ERP design.
3. Research & Discovery
Jobs To Be Done
What should I focus or attend to today?
When I am starting my day or finished with a task, I want to see what projects need my attention to move forward, so I can work on them and clear up my tasks for the day.
How do I keep everyone in the project involved and informed?
When I am managing a specific project, I want to keep everyone informed about new happenings and requests, so I can make sure everyone is in the loop and keep the project running smoothly.
At what stage is the project on currently?
When I am managing my project, I want to know what stage they are on, so I can shuffle my priorities and make a mental note to attend projects that are active.
Artifact Collection
Artifact collection was imperative to understand the flow of information from stage to stage in order to map them to the ERP. These included:
- Order tracking excel sheet
- Quotation request tracking excel sheet
- Order, Quotation, Inspection and Shipping forms
- Autocad files and versions
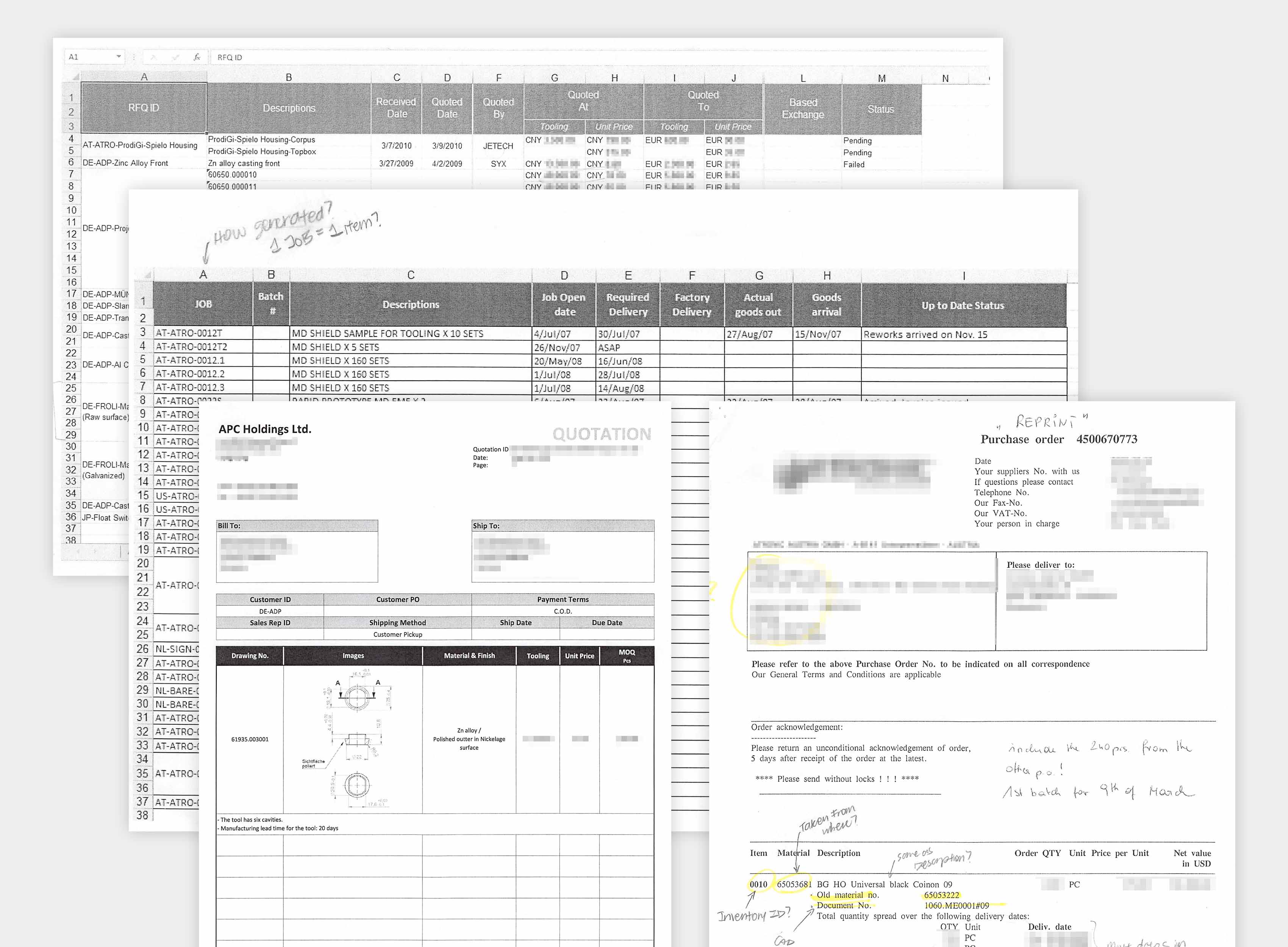
Project Lifecycle Mapping
Project life cycles were created to answer the following questions:
- Who is involved and at what stage of the project?
- What are their specific tasks?
- What are the stages of a project?
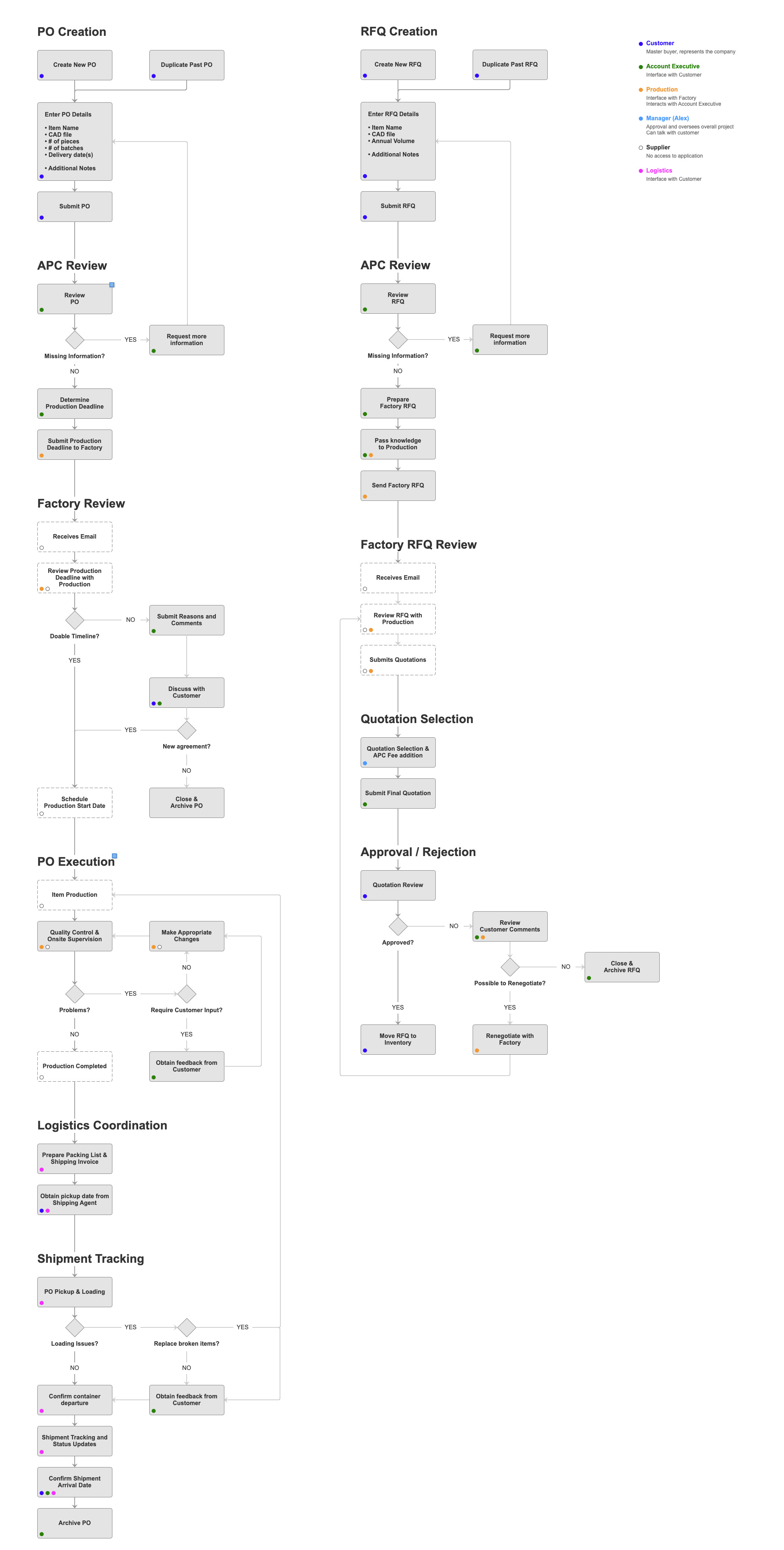
4. Brainstorming
We conducted a series of workshops with stakeholders to sketch and discuss what the ERP could start to look like.
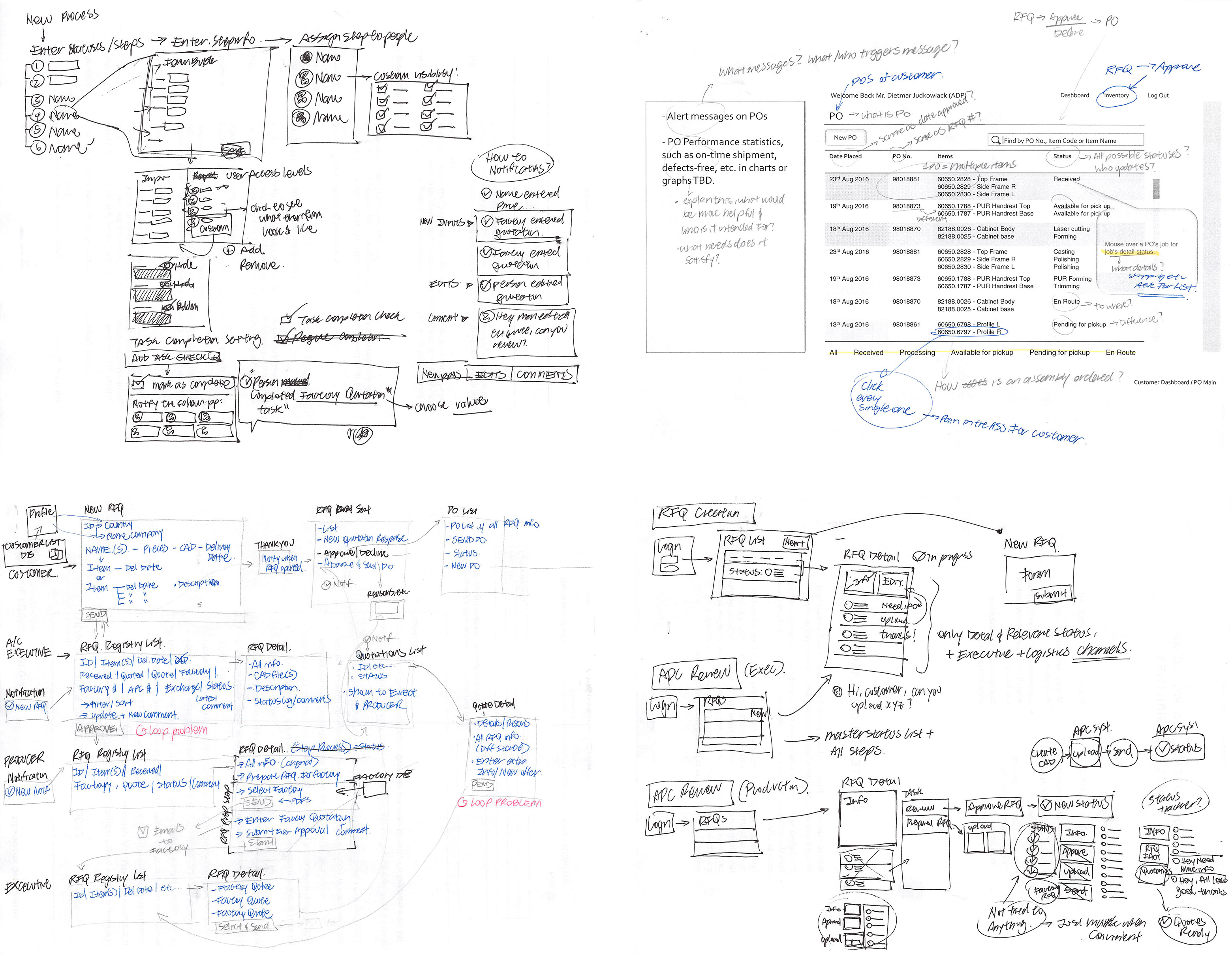
5. Recommendations
What should I focus or attend to today?
- Dashboard showcasing number of projects filterable by stages.
- Running list unread messages left by team members or customers.
- Running list of unread edits to projects such as new field entered or files uploaded.
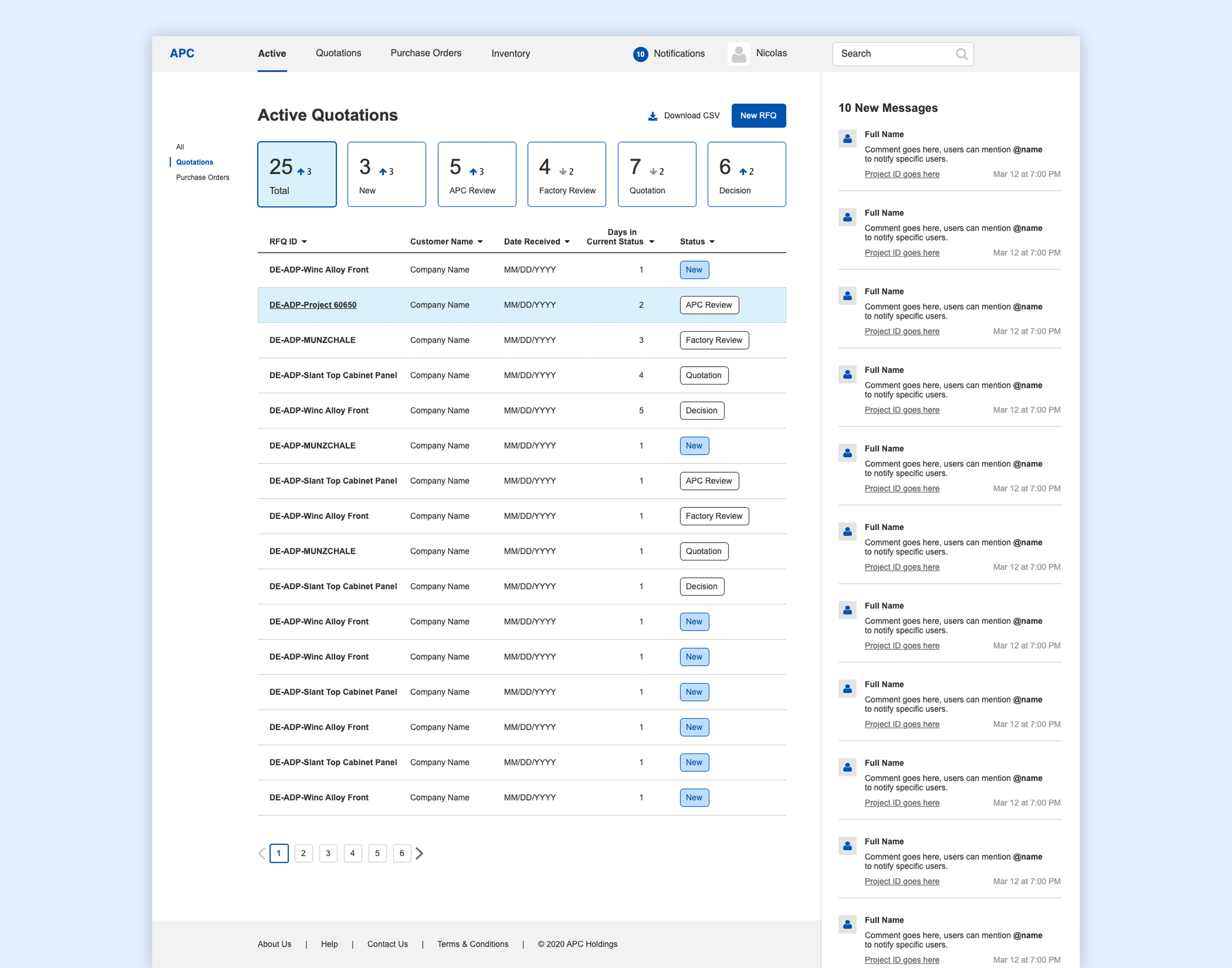
How do I keep everyone in the project involved and informed?
- Send messages to the entire team to keep members involved.
- Keep separate rooms for customer, APC team and supplier conversations.
- Track history of changes performed in the project file.
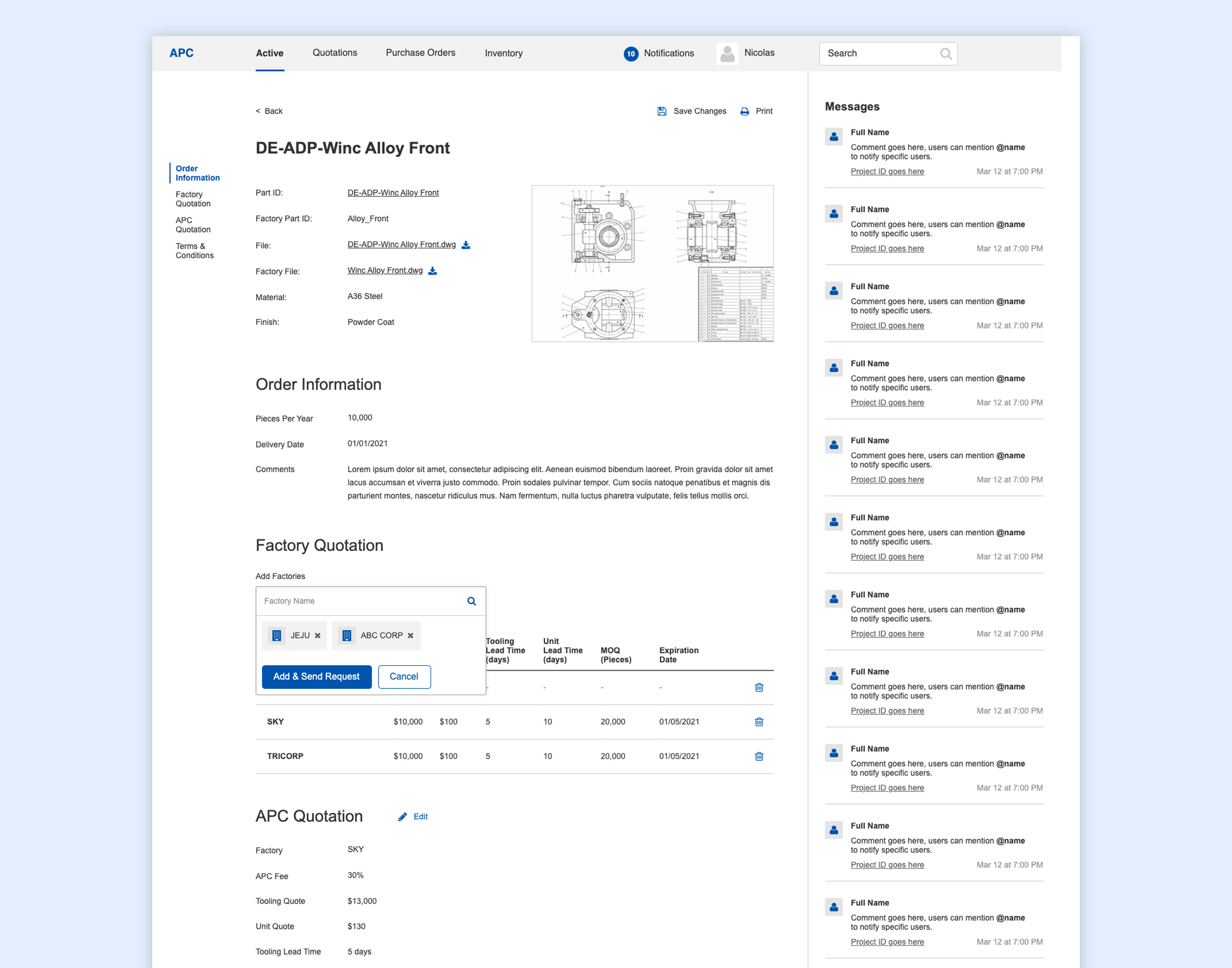
At what stage is the project currently on?
- Introduce consistent project stages to track orders.
- Track progress closely through an activity tracker.
- Individual batch tracking within the same order.
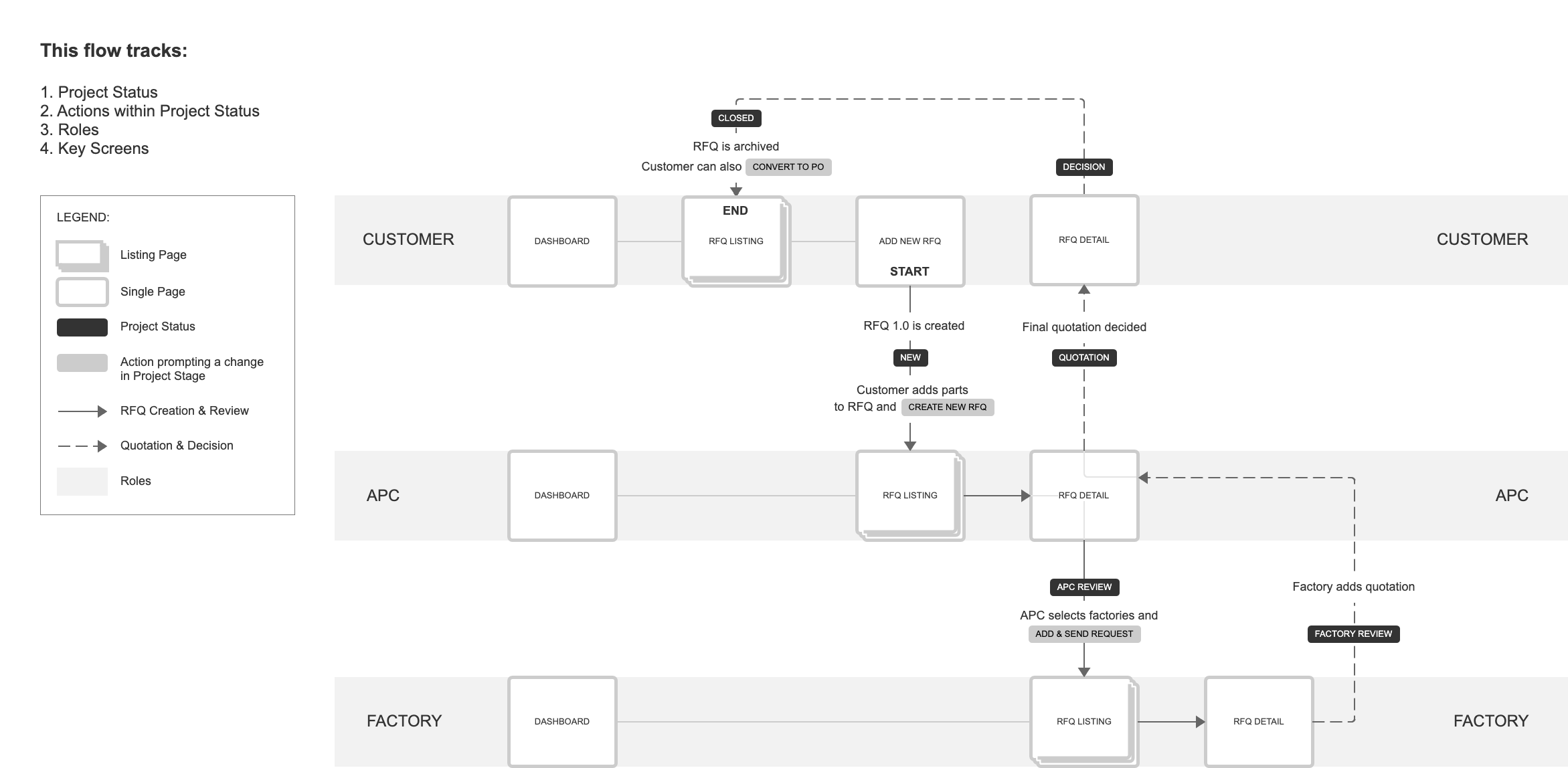
6. Challenges & Learnings
Building a tool to control all aspects of order tracking, factory production, quality control and shipping requires the team to first understand the lifecycle of the product.
The challenging part was the amount of actors involved, each completing unique tasks. Ensuring successful task completion while maintaining a coherent design system proved to be challenging as we were aiming for maximum reusability due to resource constraints.
This project was rewarding due to a complete integration between business operations and interface design. The interface serves as a layer tying all aspects of operation and maximizing efficiency. Interviews and artifact collection pieced together a map of the company's operation from start to end. Which not only helped us learn the business but also gave the client ideas about inefficiencies through extensive questioning of whys.
7. Reference Material
For a deep dive into the project, please reference the following links: